
Heat Stake Press
The project objective was to heat stake two plastic heat inserts into a plastic part. The manufacturing team requested a mechanism that was easy to use, manually actuated, and overall safe for line technicians to have on the production line table.
​
I began with a cradle to fix the part to be staked. A table-top arbor press was selected as the main mechanism for the staking. This saved us surface area on the production table and total costs. The brass insert was to be heated to the melting point of the abs + pla plastic mixture while not burning the rest of the part. This inspired a custom tip to heat and push down the brass inserts. The heating tip was designed to fit into a larger brass block to be heated by a cartridge fire rod. The fire rod's temperature could be calculated and controlled from the built-in thermocouple.

The brass block was supported by a plate and coupler attached to the arbor press' rod. Additionally, two linear rails were added as guides to further constrain the downward motion of the press. As the press moves down, the heated brass block and tips are slid down over the rails and into the part- slowly melting plastic and inserting the brass inserts.

(Not pictured: a mesh cover around the heated brass block)
Two rounds of testing were needed to find the best temperature for the cartridge fire rod. The ideal temperature was somewhere between 400 F and 450 F. This and controlling the PID loop on the heat controller made for smooth insertion and little to no plastic flashing. The image below was taken during a round of testing. Funny enough, the best way to view the heated pins was to clamp the arbor press upside down.

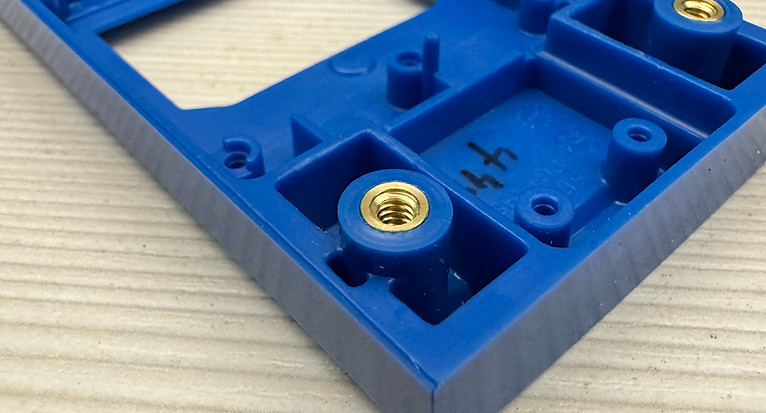
Beautiful